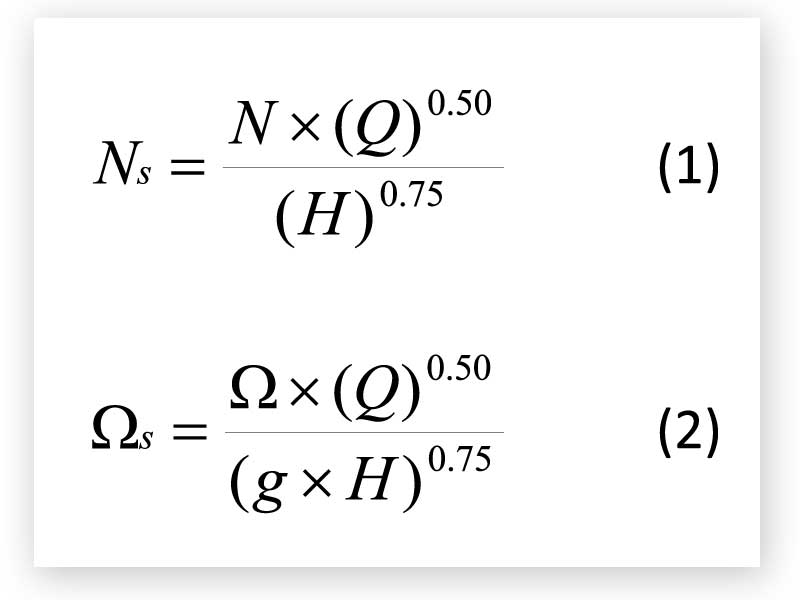
Specific Speed – Does it Matter?
Randal FermanTo the pump engineer or pump manufacturer specific speed is terrifically important. To the specifying engineer or user – maybe, maybe not.
The term specific speed comes up frequently in pump literature, in technical papers and is always covered in pump text books. It is frequently heard in pump technical banter and if one doesn’t have a concept of it he can feel like he’s listening to a foreign tongue.
Specific speed is the basic pump performance parameter derived from dimensional analysis of the three essential variables of head rise and rate of flow (at pump best efficiency point), and shaft rotational frequency (speed). Specific speed is independent of pump size and serves as a primary index or type number of pump hydraulic performance.
Equation (1) is the customary form of specific speed that still prevails. In the US, flow (Q) is in units of GPM, head (H) in feet, and speed (N) in RPM. The customary units for metric are varied. The units of flow (Q) can be in m3/h, m3/min or m3/s, the head (H) in meters, and speed (N) in RPM. Equation (2) is the dimensionless form of specific speed (Ωs) which depends upon homogeneous, consistent units, and will yield the same value whether the source units are USCS or metric. Ω is the shaft rotational frequency in radians per second and g is gravitation acceleration. The equation (2) form is gaining wider acceptance in technical works. One must always be vigilant about units when interpreting specific speed.
Here is a list of some important uses of the specific speed parameter. It is not a comprehensive listing, but it does cover the important ones.
Specific speed is used to:
- model or scale pump performance and hydraulic design
- estimate the effects of impeller trimming
- qualitatively or quantitatively relate pump performance to hydraulic geometry, shape and physical proportion
- optimize selection of the main hydraulic design geometry dimensions
- evaluate or optimize the attainable pump efficiency based on historical test experience
- evaluate the slope of curve to shutoff for head rise and for input power
- evaluate the potential for retrofitting and re-rating an existing pump for a new set of operating conditions
Even if these characteristics are of interest to the pump user, application of the specific speed parameter largely remains in the hands of the pump engineer. He uses specific speed all of the time – it’s usually the first parameter calculated and plays an important role in the pump selection process and in the initial design stages of modeling and parametric evaluation for a new pump.
The specifying engineer or end user does not normally get involved directly with considerations of specific speed. The pump manufacturer or equipment distributor receives the pump data sheet, and selects a pump and perhaps offers a few alternate options. At this point all decisions regarding specific speed have been made. Even if the specifying engineer or end user selects out of a catalogue, the decision will probably be based on features, performance, reputation, price or delivery, not on specific speed.
There are perhaps a few notable exceptions. For example, a pipeline engineer dealing with a large capacity transport system. He considers the pipeline hydraulic profile, the pump station spacing, the number of pumps per station, the driver and pump operating speeds and the number of pump stages. All of these tie in directly or indirectly with pump specific speed.
But generally, pump specific speed is not so important to the specifying engineer or to the end user. Perhaps its greatest value lies in knowing enough so that one can listen to a pump person speak without losing consciousness.
I am interested to hear your thoughts on this.
Randal Ferman, PE
6 comments
Randal sir, Thanks for the reply.
Further to your clarification, comes another doubt ! The designer needs to have clarity of the pump-type to be used for the particular application beforehand. The selection of the pump-type must then explicitely be defined by the head (and/or discharge). But, I have often come across situations where semi-axial pumps and radial pumps have been used for the same (or similar) duty. How would a designer be sure that he has selected the correct pump-type for his application ?
Saurabh,
Selection of pump type depends on performance requirements and the specific type of service. The appropriate pump type is usually known at the outset by people familiar with specifying or selecting pumps for a particular industry and service. Most of the information can be obtained from published literature in the form of engineering texts, trade publications and manufacturers’ brochures and technical data. A person relatively new to the pump business might become overwhelmed by the vast amount of such information. But there is no sense in learning how to re-invent the wheel when one can cultivate friendships with knowledgeable and experienced professionals.
Best regards,
Randal
Randal sir, Thanks for the reply.
Further to your clarification, comes another doubt ! The designer needs to have clarity of the pump-type to be used for the particular application beforehand. The selection of the pump-type must then explicitely be defined by the head (and/or discharge). But, I have often come across situations where semi-axial pumps and radial pumps have been used for the same (or similar) duty. How would a designer be sure that he has selected the correct pump-type for his application ?
Saurabh,
Optimal pump specific speed for efficiency is relatively constant over a wide range of head vs. flow. It tends to vary more with the pump geometry type. For instance, the optimal specific speed for a single suction, single stage radial discharge impeller is about nq = 50 (rpm, m3/s, m). Multistage pumps with a large shaft through the impeller eye tend to be designed with lower specific speeds. Vertical bowl type pumps are often designed in a higher range of specific speed with excellent efficiency performance.
The range of optimal efficiency is broad. Arguably one could say it is at least +/-20% from a middle, optimal value. Also, the attainable efficiency for a given specific speed is relatively constant over a wide range of head. For practical purposes it doesn’t matter if the head is 3 meters or 300 meters – the optimal specific speed, considering efficiency alone, will be the same.
So in your case, you could start with nq = 50, and with the given head and flow, calculate the speed. If the speed is acceptable, then you can move forward from that point.
I hope this helps,
Randal
Saurabh,
There is, in fact, an experience-based range of optimal specific speed for pump efficiency. Pump texts carry this information in the form of charts and sometimes best fit equations are provided. An example of such a chart and its equations is found in Pump Handbook Fourth Edition by Karassik, et al, in Chapter 2, Figure 10 and the accompanying text.
In the practical world of pump hydraulic selection, one typically deals with multiple constraints such as available motor speeds, head per stage considerations, the appropriate pump mechanical configuration, and suction performance. When these or other factors are taken into account, the choice of specific speed is often not a theoretically optimal value for efficiency. On the other hand, large transport pipelines represent a pump application example wherein choice of specific speed for high efficiency is important.
I recommend you get a copy of the above Pump Handbook or Gulich’s Centrifugal Pumps 2nd Edition, develop a spreadsheet and work out the optimal set of performance parameters.
Good luck with this,
Randal